在环保意识日益增强的时代,纸袋作为塑料的可持续替代品,重新受到欢迎。了解这些看似简单的包装袋的制造过程可以揭示一个精密、工艺和创新的世界。以下是纸袋制造的一般工艺流程:
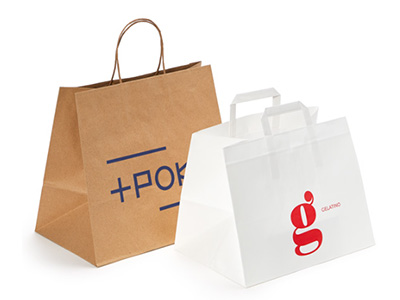
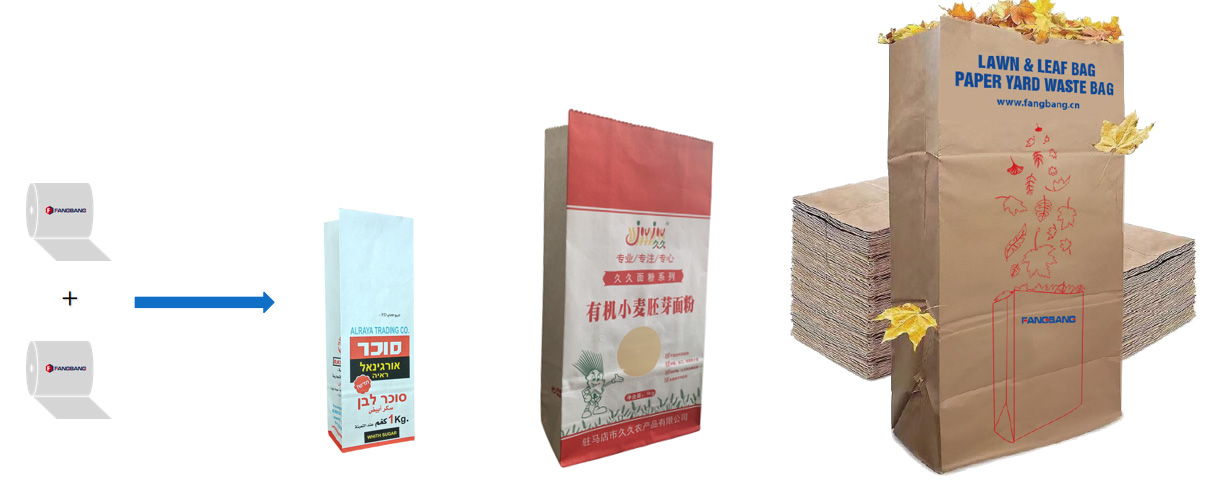
原料准备
·选择纸张:主要用牛皮纸、铜版纸、卡纸等。牛皮纸韧性好、强度高、表面粗糙;铜版纸有一定韧性、印刷色彩丰富;卡纸挺度好。
·准备辅助材料:如印刷油墨、胶水、绳子或丝带等,用于制作提手。
制浆造纸
·制浆:若使用原生木浆,则需将木材去皮、切成条状,再通过蒸煮等工序转化为木浆。也可使用再生纤维。回收的废纸经过分类、筛选、脱墨等处理,制成再生纸浆。
·造纸:将木浆与水混合制成纸浆溶液,加入碳酸钙、粘土等填料以及染料、荧光增白剂等添加剂,再通过一系列旋转和固定的刀片对纤维进行细化,以增加纸张的强度。然后将纸浆溶液送入造纸机,在造纸机中将水分挤出、干燥,并压成大卷或大张的纸张。
印刷
· 设计制版:根据客户需求设计纸袋的图案、文字等内容,制作印版。
·印刷:通过胶印、柔版印刷、数码印刷等方式将设计好的图案、文字印在纸张上。印刷时要注意控制水墨平衡,调整设备状态,保证印刷质量。我公司配备柔版印刷机,可以很好地完成这一工序。
纸袋成型
·裁切:将印刷好的纸张,按照纸袋的尺寸进行裁切,得到合适的纸张。
·折叠粘贴:用机器或手工将纸张折叠成纸袋形状,用胶水或热封将纸袋的侧面和底部牢固粘贴。
· 制作提手:根据纸袋的设计要求制作并安装提手,提手可用纸、绳、丝带等制成,通过粘贴、缝制或冲孔等方式固定在纸袋上。我们的纸袋机兼容多种提手成型工艺,采用对称可调式双模板结构,一次性生产出带提手的方底纸袋,是理想的纸袋成型设备。
表面处理
·覆膜:在纸袋表面覆上一层透明的塑料薄膜,如高光膜或者哑光膜,增加纸袋的光泽度、防水性、耐磨性等。
·烫金/烫银:利用烫金或烫银技术,在纸袋表面增加金属光泽的图案或文字,提升纸袋的档次和美观度。
·上光:在纸袋表面涂上一层光油,增加纸袋的光泽度和质感,同时也起到一定的保护作用。
质量检验和包装
·品质检验:对纸袋进行全面的品质检验,包括外观检验、尺寸测量、印刷质量检验、粘合牢固度检验等,确保纸袋符合质量标准。
·包装:将检验合格的纸袋进行包装,一般采用纸箱或塑料薄膜包装,方便运输和储存。
纸袋的制造过程是艺术与科学的完美结合,融合了原材料专业知识、机械精度和创意技能。随着消费者越来越多地寻求可持续的包装选择,纸袋行业不断发展,我们也在努力改进其工艺,以满足功能性、美观性和生态意识的需求。如果您在纸袋制造方面有任何需求,您可以联系我们,我们将提供优质的解决方案来解决问题。