在包装行业漫长而波澜壮阔的发展历程中,纸袋机就像一颗耀眼的明星,但它在前进的征程上也陷入泥潭,挑战重重,机遇与困难交织,勾勒出这个行业的跌宕起伏,只有探寻它的历史轨迹,才能准确把握当下的症结,预判未来的走向。
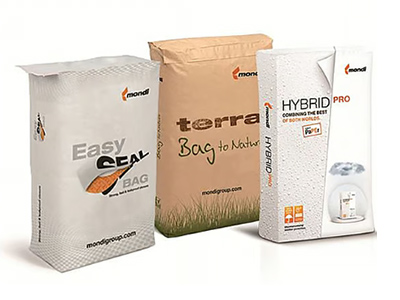
19世纪下半叶,工业革命的余烬催生了第一代纸袋机,萌芽于欧美的手工作坊中。当时,简单的机械结构搭配原始的手摇传动,犹如蹒跚学步的幼儿,难以开启纸袋机械化生产之旅。工匠们手工裁纸,费力折叠、粘合,再慢慢转动手摇轮带动简易模具成型。纸袋日产量仅有数十只,且款式有限、质地脆弱,勉强支撑小商贩对零碎物品的包装需求。但这颗创新之火,点燃了随后的燎原之火。
时间来到上世纪三十年代,电气技术的曙光初现,纸袋机摆脱了人力的束缚。电机驱动的引入让设备拥有了稳定的运行动力,生产效率也随之上升,小型工厂的雏形逐渐显现。这一阶段,纸袋机增加了基本的调速装置,可以精细调整生产节奏;简易的印刷模块出现,让纸袋初步呈现出品牌标识。虽然工艺粗糙,但足以在零售货架上脱颖而出,吸引消费者的眼球,悄然拓展了商业包装的边界。
第二次世界大战结束后,全球经济复苏的号角吹响,消费市场井喷,成为纸袋机跨越式发展的催化剂。1960年代起,机械化、自动化概念深入渗透,凸轮机构、连杆传动,优化纸袋成型精度;光电传感器开始展现锋芒,实时监控纸张走向,降低废品率。热熔胶技术的革新是关键的里程碑,黏度强、干燥速度快的热熔胶取代传统糊状物,使纸袋牢固高效地粘合,不怕运输颠簸,为批量长途运输包装奠定基础。
20世纪末至21世纪初,计算机、信息技术浪潮汹涌澎湃,纸袋机陷入智能化的漩涡。PLC控制系统全面普及,配备人机交互触摸屏,参数设定随心掌控;CAD(计算机辅助设计)技术使纸袋款式设计、复杂结构、精美图案一键生成,成品直接从生产端输出。同时,随着国际物流、电子商务的兴起,海量的邮寄需求倒逼纸袋机产能升级,高速生产线应运而生。每分钟都有数百只纸袋被生产出来,涌入全球各地的仓库。
回首往昔辉煌,再看当下,纸袋机行业陷入泥潭,研发投入居高不下,成为悬在企业头上的“达摩克利斯之剑”,新技术探索、跨领域融合需要海量资金,从智能算法优化、新材料适配,到量子点打印对接,中小厂商束手无策,无法突破技术壁垒,产品高度同质化,低价竞争猖獗。
原材料市场的动荡加剧了困境。森林资源的稀缺、环保伐木的限制,导致优质纸张的价格犹如过山车般跌宕起伏。化工原料受国际原油波动影响,胶水、油墨等成本飘忽不定,企业成本控制成为空谈,利润被大幅压缩。更为艰难的是全球供应链的“肠梗阻”。关键零部件进口受阻、芯片供应使智能控制系统陷入瘫痪、高精度电机短缺导致产能归零,售后维修也受制于技术和远程协作。故障设备成为“废铁”,停工损失触目惊心。
市场需求端同样风起云涌,消费者环保意识的觉醒催生出高标准,纸袋既要设计美观时尚,符合时尚审美;又要多功能,防水、承重、保鲜。在电商促销潮订单冲击下,纸袋机产能配置捉襟见肘,物流延误、供货不足等情况时有发生。
在这场创新与挑战的生死较量中,纸袋机企业唯有结盟,打破僵局,才能生存。产学研深度融合,分担研发成本,攻克技术壁垒;为本土供应链构筑“护城河”,化解进口依赖风险;精准把握消费者心理,灵活生产应对。唯有如此,才能把握纸袋机包装利刃,披荆斩棘,走出一条产业复兴之路。